Tolerances
Dimensional tolerances of cut contours. Cutting is in accordance with the ISO9013 norm, unless stated otherwise in the table below.
Work piece thickness (mm) | Allowable tolerances for the range of nominal measurements (mm) | |||||||
---|---|---|---|---|---|---|---|---|
> 0 < 3 | ≥ 3 < 10 | ≥ 10 < 35 | ≥ 35 < 125 | ≥ 125 < 315 | ≥ 315 < 1000 | ≥ 1000 < 2000 | ≥ 2000 | |
> 0,5 ≤ 1 | ± 0,2 | ± 0,2 | ± 0,2 | ± 0,2 | ± 0,2 | ± 0,3 | ± 0,4 | ± 0,65 |
> 1 ≤ 3 | ± 0,2 | ± 0,2 | ± 0,2 | ± 0,25 | ± 0,25 | ± 0,35 | ± 0,4 | ± 0,65 |
> 3 ≤ 6 | ± 0,2 | ± 0,2 | ± 0,25 | ± 0,25 | ± 0,3 | ± 0,4 | ± 0,45 | ± 0,7 |
> 6 ≤ 10 | - | ± 0,25 | ± 0,3 | ± 0,3 | ± 0,35 | ± 0,45 | ± 0,55 | ± 0,75 |
> 10 ≤ 15 | - | ± 0,3 | ± 0,35 | ± 0,35 | ± 0,45 | ± 0,55 | ± 0,65 | ± 0,85 |
> 15 ≤ 20 | - | ± 0,4 | ± 0,4 | ± 0,4 | ± 0,55 | ± 0,75 | ± 0,85 | ± 1,2 |
> 20 ≤ 25 | - | ± 0,45 | ± 0,45 | ± 0,5 | ± 0,7 | ± 0,9 | ± 1,1 | ± 1,6 |
Discoloration of material after laser cutting
Depending on the material and contour of the laser parts, discoloration of the material may occur during laser cutting. This occurs especially with small geometries or contours and narrow webs, because the heat of the laser cannot be sufficiently dissipated in these areas. Discoloration is a common phenomenon and can only be removed by grinding.
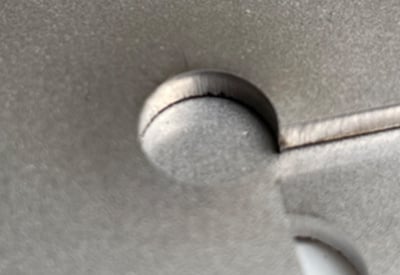
Laser splashes and soot
Depending on the material and sheet thickness, spatter or soot may occur on the underside of laser parts during laser cutting. This can be caused by laser insertion, part geometry, very small contours and part positioning on the laser blades. Depending on the material, soot cannot always be avoided, but it can be easily removed by simply wiping it off.
The difference between nitrogen and oxygen
Laser cutting with nitrogen | Laser cutting with oxygen | |
Advantages | Clean cutting edge with minimal burning or discoloration | Cost-effective |
Low heat-affected zone | High cutting speed (for aluminum) | |
Disadvantages | Faster burr formation on tight/small contours | Discoloration and oxidation possible |
Limited choice of materials | Wide heat-affected zone |
Results by laser cutting with oxygen
Results by laser cutting with nitrogen
Distortion during laser cutting
For long or large parts with many small recesses or contours provided with fine lines on the surface, heat distortion is often inevitable. It is important to take this into account when designing. Many and/or strong concentrated engravings also cause warping of the product.
Without edge finishing
Without edge finishing
With edge finishing
Thread tapping
Thread tapping at 247TailorSteel is possible within the following guidelines:
- Flat and bent plates.
- Maximum product sizes of 1000x1000 mm or 2000x500 mm.
- A maximum product weight of 40 kg.
The table below shows the various M sizes with corresponding bore diameter, pitch (the distance travelled by a screw in one revolution) and minimum and maximum thickness of the plate.
Draw the holes in your drawing programme with the correct diameter. In Sophia® , tick which holes can be tapped.
Tapped hole (M) | Drill diameter (mm) | Pitch (mm) | Minimum thickness (mm) | Maximum thickness (mm) |
|||
Steel (nitrogen) | Steel (oxygen) | Stainless steel | Aluminium | ||||
M3 |
2,5 |
0,50 |
1,0 |
4 |
6 |
5 |
4 |
M4 |
3,3 |
0,70 |
1,4 |
4 |
6 |
12 |
4 |
M5 |
4,2 |
0,80 |
1,6 |
5 |
6 |
15 |
6 |
M6 |
5 |
1,00 |
2,0 |
6 |
8 |
20 |
8 |
M8 |
6,8 |
1,25 |
2,4 |
8 |
15 |
20 |
8 |
M10 |
8,5 |
1,50 |
3,0 |
8 |
15 |
20 |
10 |
M12 |
10,2 |
1,75 |
3,0 |
8 |
15 |
20 |
10 |
M14 |
12 |
2,00 |
4,0 |
8 |
20 |
20 |
10 |
M16 |
14 |
2,00 |
4,0 |
8 |
20 |
20 |
10 |
M18 |
15,5 |
2,50 |
5,0 |
8 |
25 |
20 |
10 |
M20 |
17,5 |
2,50 |
5,0 |
8 |
25 |
20 |
10 |
M22 |
19,5 |
2,50 |
5,0 |
8 |
25 |
20 |
10 |
M24 |
21 |
3,00 |
6,0 |
8 |
25 |
20 |
10 |