Toleranzen
Toleranzen beim Aufmaß von Schnittkonturen. Falls es in nachfolgender Tabelle nicht anders angegeben ist, schneiden wir der Norm ISO9013 entsprechend.
Dicke des Werkstücks (mm) | Zulässige Abweichungen für den Bereich der Nenngrößen (mm) | |||||||
---|---|---|---|---|---|---|---|---|
> 0 < 3 | ≥ 3 < 10 | ≥ 10 < 35 | ≥ 35 < 125 | ≥ 125 < 315 | ≥ 315 < 1000 | ≥ 1000 < 2000 | ≥ 2000 | |
> 0,5 ≤ 1 | ± 0,2 | ± 0,2 | ± 0,2 | ± 0,2 | ± 0,2 | ± 0,3 | ± 0,4 | ± 0,65 |
> 1 ≤ 3 | ± 0,2 | ± 0,2 | ± 0,2 | ± 0,25 | ± 0,25 | ± 0,35 | ± 0,4 | ± 0,65 |
> 3 ≤ 6 | ± 0,2 | ± 0,2 | ± 0,25 | ± 0,25 | ± 0,3 | ± 0,4 | ± 0,45 | ± 0,7 |
> 6 ≤ 10 | - | ± 0,25 | ± 0,3 | ± 0,3 | ± 0,35 | ± 0,45 | ± 0,55 | ± 0,75 |
> 10 ≤ 15 | - | ± 0,3 | ± 0,35 | ± 0,35 | ± 0,45 | ± 0,55 | ± 0,65 | ± 0,85 |
> 15 ≤ 20 | - | ± 0,4 | ± 0,4 | ± 0,4 | ± 0,55 | ± 0,75 | ± 0,85 | ± 1,2 |
> 20 ≤ 25 | - | ± 0,45 | ± 0,45 | ± 0,5 | ± 0,7 | ± 0,9 | ± 1,1 | ± 1,6 |
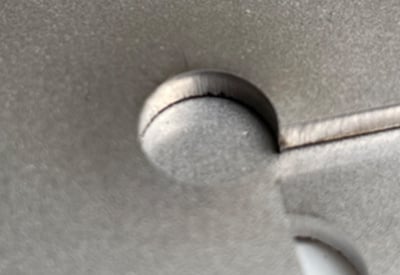
Laserspritzer, Ruß und Aufschmelzen
Beim Laserschneiden können je nach Material und Blechdicke Spritzer oder Ruß auf der Unterseite der Laserteile auftreten. Die Ursachen dafür können der Lasereinstich, die Bauteilgeometrie, sehr kleine Konturen und die Positionierung der Bauteile auf den Laserlamellen sein. Der Ruß lässt sich je nach Material nicht immer vermeiden, lässt sich jedoch einfach abwischen.
Unterschied zwischen Stickstoff und Sauerstoff
Laserschneiden mit Stickstoff | Laserschneiden mit Sauerstoff | |
Vorteile | Saubere Schnitt ohne Verbrennung oder Verfärbung | Kosteneffizient |
Geringe Wärmeeinflusszone | Hohe Schnittgeschwindigkeit | |
Nachteile | Schnellere Gratbildung bei engen/kleinen Konturen | Verfärbung und Oxidation möglich |
Begrenzte Materialvielfalt | Breitere Wärmeeinflusszone |
Ergebnisse beim Laserschneiden mit Sauerstoff
Ergebnisse beim Laserschneiden mit Stickstoff
Verzug beim Laserschneiden
Bei langen/großen Teilen und vielen kleinen Ausschnitten oder Konturen mit kleinen Stegen auf einer Fläche kommt es häufig zu Wärmeverzug, der nicht zu vermeiden ist und bei der Konstruktion berücksichtigt werden muss.
Ohne Kantenbearbeitung
Ohne Kantenbearbeitung
Mit Kantenbearbeitung
Gewindeschneiden
Gewindeschneiden ist bei 247TailorSteel im Rahmen der folgenden Richtlinien möglich:
- Flache und gebogene Bleche.
- Maximale Produktgrößen von 1000x1000 mm oder 2000x500 mm.
- Ein maximales Produktgewicht von 40 kg.
Die nachstehende Tabelle zeigt die verschiedenen Größen von metrischen Gewinden mit dem entsprechenden Bohrungsdurchmesser, der Steigung (Abstand zwischen zwei Gewindegängen) und der Mindest- und Höchstdicke der Platte.
Zeichnen Sie die Bohrungen in Ihrem Zeichenprogramm mit dem richtigen Durchmesser des Kernloches ein. Wählen Sie in Sophia® aus, welche Löcher mit einem Gewinde versehen wollen. Lesen Sie alles über Gewindeschneiden in unserem Feature Friday.
Gewindegröβe (M) | Kernlochdurchmesser (mm) | Steigung (mm) | Minimale Dicke (mm) | Maximale Dicke (mm) |
|||
Stahl (Stickstoff) | Stahl (Sauerstoff) | Edelstahl | Aluminium | ||||
M3 |
2,5 |
0,50 |
1,0 |
4 |
6 |
5 |
4 |
M4 |
3,3 |
0,70 |
1,4 |
4 |
6 |
12 |
4 |
M5 |
4,2 |
0,80 |
1,6 |
5 |
6 |
15 |
6 |
M6 |
5 |
1,00 |
2,0 |
6 |
8 |
20 |
8 |
M8 |
6,8 |
1,25 |
2,4 |
8 |
15 |
20 |
8 |
M10 |
8,5 |
1,50 |
3,0 |
8 |
15 |
20 |
10 |
M12 |
10,2 |
1,75 |
3,0 |
8 |
15 |
20 |
10 |
M14 |
12 |
2,00 |
4,0 |
8 |
20 |
20 |
10 |
M16 |
14 |
2,00 |
4,0 |
8 |
20 |
20 |
10 |
M18 |
15,5 |
2,50 |
5,0 |
8 |
25 |
20 |
10 |
M20 |
17,5 |
2,50 |
5,0 |
8 |
25 |
20 |
10 |
M22 |
19,5 |
2,50 |
5,0 |
8 |
25 |
20 |
10 |
M24 |
21 |
3,00 |
6,0 |
8 |
25 |
20 |
10 |
Changelog
Datum | Art der Bearbeitung | Beschreibung |
25.03.2025 |
|
Lieferspezifikationen für Gewindeschneiden hinzugefügt |
18.12.2024 |
|
Lieferspezifikationen zur Kantenabrundung und aktualisierte Informationen zum Kantenbrechen hinzugefügt |
24.05.2024 |
|
Seite veröffentlicht |