General
- Maximum sheet thickness for steel is 12 mm.
- Maximum sheet thickness for stainless steel is 10 mm.
- Maximum sheet thickness for aluminium is 12 mm.
- Maximum weight is 75 kg.
- Maximum dimensions are 2980 x 1480 mm.
- Maximum stop size is 1150 mm.
- These dimensions are all in relation to a 90° angle. If the product contains one or more sharp bends, use the dimensions from the sharp tables for all bends in the product.
- An edging product must always have a bending radius.
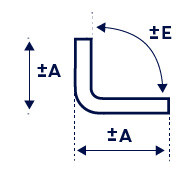
S. | A | B | C | D | E | F |
t/m 3 mm | ± 0,2 mm | ± 0,5 mm | ± 0,8 mm | ± 0,5 mm | ± 0,5° | 15′/100MM |
4 mm | ± 0,3 mm | ± 0,6 mm | ± 1,2 mm | ± 0,6 mm | ± 0,5° | 15′/100MM |
5 t/m 6 mm | ± 0,4 mm | ± 0,8 mm | ± 1,6 mm | ± 0,8 mm | ± 0,5° | 15′/100MM |
8 mm | ± 0,5 mm | ± 1 mm | ± 2 mm | ± 1 mm | ± 0,5° | 15′/100MM |
10 mm | ± 0,8 mm | ± 1,6 mm | ± 3,2 mm | ± 1,6 mm | ± 0,5° | 15′/100MM |
Checker plate | 2 mm | 1,5° | ||||
Hemming | ± 1 mm | 0 tot 0,5 x sheet thickness |
Material thickness | Steel | Stainless steel | Aluminum | High-strength steel |
0,8 mm | 1,39 | 1,56 | - | - |
1 mm | 1,40 | 1,58 | 1,27 | - |
1,25 mm | 1,42 | 1,57 | - | - |
1,5 mm | 1,65 | 1,90 | 1,47 | - |
2 mm | 1,88 | 2,22 | 1,67 | - |
2,5 mm | 2,41 | 2,94 | 2,11 | - |
3 mm | 2,75 | 3,75 | 2,50 | - |
4 mm | 3,02 | 4,48 | 3,30 | - |
5 mm | 3,62 | 7,82 | 4,07 | - |
6 mm | 4,62 | 11,91 | 5,34 | - |
8 mm | 8,00 | 11,64 | 8,12 | 8,00 |
10 mm* | 8,00 | 15,00 | 18,89 | 8,23 |
12 mm* | 7,83 | - | - | 7,02 |
*For thicknesses of 10 mm and 12 mm, it is not possible to bend full lengths. Please contact Customer Service for more information.
Material thickness | Steel | Stainless steel | Aluminum |
0,8 mm | 1,41 | 1,72 | - |
1 mm | 1,35 | 1,62 | 1,28 |
1,25 mm | 1,27 | 1,52 | - |
1,5 mm | 1,19 | 1,42 | 1,12 |
2 mm | 1,30 | 1,59 | 1,22 |
2,5 mm | 1,73 | 2,17 | 1,61 |
3 mm | 2,51 | 3,73 | 2,86 |
4 mm | 2,24 | 3,28 | 2,48 |
5 mm | 2,45 | 5,44 | 2,70 |
6 mm | 3,08 | 8,78 | 3,53 |
8 mm | 4,74 | - | 4,33 |
This is the minimum overlay of the sheet on the mold that is necessary to perform the bending. The minimum leg length (s) is determined by the sheet thickness.
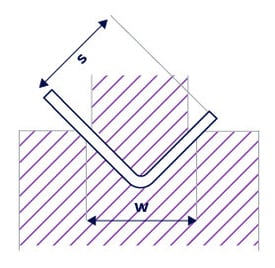
90 Degrees
Thickness | Groove width (w) | Leg length (s) |
0,63 mm | 8 mm | 5,60 mm |
0,8 mm | 8 mm | 5,70 mm |
0,88 mm | 8 mm | 5,80 mm |
0,9 mm | 8 mm | 5,80 mm |
1 mm | 8 mm | 5,90 mm |
1,25 mm | 8 mm | 6,10 mm |
1,5 mm | 10 mm | 7,50 mm |
2 mm | 12 mm | 9,10 mm |
2,5 mm | 16 mm | 12,00 mm |
3 mm | 16 mm | 12,40 mm |
4 mm | 24 mm | 17,70 mm |
5 mm | 30 mm | 22,60 mm |
6 mm | 40 mm | 29,60 mm |
8 mm | 60 mm | 43 mm |
10 mm* | - | 44 mm |
12 mm* | - | 56,50 mm |
*For thicknesses of 10 mm and 12 mm, it is not possible to bend full lengths. Please contact Customer Service for more information.
Thickness | Groove width (w) | Leg length (s) |
0,63 mm | - | - |
0,8 mm | 8 mm | 5,70 mm |
0,88 mm | - | - |
0,9 mm | - | - |
1 mm | 8 mm | 5,90 mm |
1,25 mm | 8 mm | 6,10 mm |
1,5 mm | 10 mm | 7,60 mm |
2 mm | 12 mm | 9,20 mm |
2,5 mm | 16 mm | 12,10 mm |
3 mm | 20 mm | 15,00 mm |
4 mm | 24 mm | 17,90 mm |
5 mm | 40 mm | 29,20 mm |
6 mm | 60 mm | 41,80 mm |
8 mm | - | 43,10 mm |
10 mm* | - | 57 mm |
12 mm* | - | - |
*For thicknesses of 10 mm and 12 mm, it is not possible to bend full lengths. Please contact Customer Service for more information.
Thickness | Groove width (w) | Leg length (s) |
0,63 mm | - | - |
0,8 mm | - | - |
0,88 mm | - | - |
0,9 mm | - | - |
1 mm | - | - |
1,25 mm | - | - |
1,5 mm | 12 mm | 8,70 mm |
2 mm | 16 mm | 11,50 mm |
2,5 mm | - | - |
3 mm | 24 mm | 16,80 mm |
4 mm | 30 mm | 21,70 mm |
5 mm | 40 mm | 28,70 mm |
6 mm | 40 mm | 29,35 mm |
8 mm | 60 mm | 53,20 mm |
10 mm* | - | 55 mm |
12 mm* | - | 56,50 mm |
*For thicknesses of 10 mm and 12 mm, it is not possible to bend full lengths. Please contact Customer Service for more information.
Sharp
Thickness | Groove width (w) | Leg length (s) |
0,63 mm | 10 mm | 9,70 mm |
0,8 mm | 10 mm | 9,80 mm |
0,88 mm | 10 mm | 9,90 mm |
0,9 mm | 10 mm | 9,90 mm |
1 mm | 10 mm | 10,00 mm |
1,25 mm | 10 mm | 10,15 mm |
1,5 mm | 10 mm | 10,30 mm |
2 mm | 12 mm | 12,40 mm |
2,5 mm | 16 mm | 15,25 mm |
3 mm | 24 mm | 21,30 mm |
4 mm | 24 mm | 22,00 mm |
5 mm | 30 mm | 22,60 mm |
6 mm | 40 mm | 29,55 mm |
8 mm | 60 mm | 42,35 mm |
*Please note: If the product contains one or more sharp bends, take the dimensions from the sharp tables for all bends in the product.
Thickness | Groove width (w) | Leg length (s) |
0,63 mm | - | - |
0,8 mm | 10 mm | 9,90 mm |
0,88 mm | - | - |
0,9 mm | - | - |
1 mm | 10 mm | 10,10 mm |
1,25 mm | 10 mm | 10,20 mm |
1,5 mm | 10 mm | 10,40 mm |
2 mm | 12 mm | 12,45 mm |
2,5 mm | 16 mm | 15,35 mm |
3 mm | 24 mm | 21,50 mm |
4 mm | 24 mm | 22,20 mm |
5 mm | 40 mm | 29,20 mm |
6 mm | 60 mm | 41,80 mm |
8 mm | - | - |
*Please note: If the product contains one or more sharp bends, take the dimensions from the sharp tables for all bends in the product.
Thickness | Groove width (w) | Leg length (s) |
0,63 mm | - | - |
0,8 mm | - | - |
0,88 mm | - | - |
0,9 mm | - | - |
1 mm | - | - |
1,25 mm | - | - |
1,5 mm | 12 mm | 11,90 mm |
2 mm | 12 mm | 12,30 mm |
2,5 mm | - | - |
3 mm | 24 mm | 21,15 mm |
4 mm | 30 mm | 21,90 mm |
5 mm | 40 mm | 28,70 mm |
6 mm | 40 mm | 29,35 mm |
8 mm | 60 mm | 42,40 mm |
*Please note: If the product contains one or more sharp bends, take the dimensions from the sharp tables for all bends in the product.
Maximum bending lenght
The maximum force that the available bendingmachines at 247TailorSteel can apply to a product is not sufficient to bend a 3-metre length for all material thicknesses. Therefore, Sophia® checks the maximum bending line length for all materials and material thicknesses by the amount of force required for the bending lines to be edged, according to the table below:
Note:
- The maximum product length remains leading when checking in Sophia®, due to the sheet dimensions.
Material | Sheet thickness (mm) | Bending length* (mm) |
All materials 8mm | < 8 mm | 3350 mm |
AISI 304 | 8 mm | 2477 mm |
AISI 316 | 8 mm | 2471 mm |
S235 | 8 mm | 2459 mm |
S355 | 8 mm | 2784 mm |
Corten A | 8 mm | 2784 mm |
S420 | 8 mm | 2637 mm |
S700 | 8 mm | 1794 mm |
Aluminum | 8 mm | 2980 mm |
AISI 304 | 10 mm | 2115 mm |
AISI 316 | 10 mm | 2107 mm |
S235 | 10 mm | 2340 mm |
S355 | 10 mm | 2380 mm |
S420 | 10 mm | 2254 mm |
Aluminum | 10 mm | 2980 mm |
AISI 304 | 12 mm | 1460 mm |
AISI 316 | 12 mm | n.v.t. |
S235 | 12 mm | 2048 mm |
S355 | 12 mm | 1650 mm |
S420 | 12 mm | 1564 mm |
Aluminum | 12 mm | 2980 mm |
90 Degrees
Sheet thickness | Groove width (w) | Leg length (x) |
0,63 mm | 8 mm | 7,80 mm |
0,8 mm | - | 8,15 mm |
0,88 mm | 8 mm | 8,30 mm |
0,9 mm | 8 mm | 8,30 mm |
1 mm | 8 mm | 8,50 mm |
1,25 mm | 8 mm | 8,95 mm |
1,5 mm | 8 mm | 10,65 mm |
2 mm | 12 mm | 13,80 mm |
2,5 mm | 16 mm | 18,80 mm |
3 mm | 16 mm | 20,10 mm |
4 mm | 24 mm | 26,15 mm |
5 mm | 30 mm | 34,65 mm |
6 mm | 40 mm | 42,90 mm |
8 mm | 60 mm | 63 mm |
10 mm* | - | 65 mm |
12 mm* | - | 79 mm |
*For thicknesses of 10 mm and 12 mm, it is not possible to bend full lengths. Please contact Customer Service for more information.
Thickness | Groove width (w) | Leg length (x) |
0,63 mm | - | - |
0,8 mm | 8 mm | 8,35 mm |
0,88 mm | - | - |
0,9 mm | - | - |
1 mm | 8 mm | 8,70 mm |
1,25 mm | 8 mm | 9,15 mm |
1,5 mm | 10 mm | 10,95 mm |
2 mm | 12 mm | 14,20 mm |
2,5 mm | 16 mm | 19,45 mm |
3 mm | 20 mm | 24,75 mm |
4 mm | 24 mm | 27,40 mm |
5 mm | 40 mm | 44,10 mm |
6 mm | 60 mm | 63,20 mm |
8 mm | - | 66,30mm |
10 mm* | - | 84 mm |
12 mm* | - | - |
*For thicknesses of 10 mm and 12 mm, it is not possible to bend full lengths. Please contact Customer Service for more information.
Thickness | Groove width (w) | Leg length (x) |
0,63 mm | - | - |
0,8 mm | - | - |
0,88 mm | - | - |
0,9 mm | - | - |
1 mm | - | - |
1,25 mm | - | - |
1,5 mm | 12 mm | 12,30 mm |
2 mm | 12 mm | 13,40 mm |
2,5 mm | - | - |
3 mm | 24 mm | 23,45 mm |
4 mm | 30 mm | 31,80 mm |
5 mm | 40 mm | 40,40 mm |
6 mm | 40 mm | 41,15 mm |
8 mm | 60 mm | 70,40mm |
10 mm* | - | 76 mm |
12 mm* | - | 79 mm |
*For thicknesses of 10 mm and 12 mm, it is not possible to bend full lengths. Please contact Customer Service for more information.
Sharp
Thickness | Groove width (w) | Leg length (x) |
0,63 mm | 10 mm | 18,00 mm |
0,8 mm | 10 mm | 18,25 mm |
0,88 mm | 10 mm | 18,40 mm |
0,9 mm | 10 mm | 18,40 mm |
1 mm | 10 mm | 18,60 mm |
1,25 mm | 10 mm | 19,00 mm |
1,5 mm | 10 mm | 19,40 mm |
2 mm | 12 mm | 20,65 mm |
2,5 mm | 16 mm | 25,80 mm |
3 mm | 16 mm | 34,95 mm |
4 mm | 24 mm | 36,50 mm |
5 mm | 30 mm | 40,40 mm |
6 mm | 40 mm | 42,90 mm |
8 mm | 60 mm | 62,20 mm |
Thickness | Groove width (w) | Leg length (x) |
0,63 mm | - | - |
0,8 mm | 10 mm | 18,60 mm |
0,88 mm | - | - |
0,9 mm | - | - |
1 mm | 10 mm | 19,00 mm |
1,25 mm | 10 mm | 19,40 mm |
1,5 mm | 10 mm | 19,80 mm |
2 mm | 12 mm | 21,15 mm |
2,5 mm | 16 mm | 26,55 mm |
3 mm | 20 mm | 36,05 mm |
4 mm | 24 mm | 37,60 mm |
5 mm | 40 mm | 44,10 mm |
6 mm | 60 mm | 63,20 mm |
8 mm | - | - |
Thickness | Groove width (w) | Leg length (x) |
0,63 mm | - | - |
0,8 mm | - | - |
0,88 mm | - | - |
0,9 mm | - | - |
1 mm | - | - |
1,25 mm | - | - |
1,5 mm | 12 mm | 18,95 mm |
2 mm | 12 mm | 20,15 mm |
2,5 mm | - | - |
3 mm | 24 mm | 33,75 mm |
4 mm | 30 mm | 35,45 mm |
5 mm | 40 mm | 40,35 mm |
6 mm | 40 mm | 41,15 mm |
8 mm | 60 mm | 60 mm |
Due to the rebound of the material, the sheet must always be bent a bit farther than the angle indicated. The tools have a maximum angle of 30˚, which allows for bends of up to 37˚ when you take the rebound into account. The minimum angle to be bent is 175˚.
Steel and aluminum
All types, except checker plate**
Thickness | Bend angle |
t/m 4 mm | 37° t/m 175° |
5 mm t/m 8 mm | 67° t/m 175° |
10 mm* | 67° t/m 175° |
12 mm* | 85° t/m 175° |
*For thicknesses of 10 mm and 12 mm, it is not possible to bend full lengths. Please contact Customer Service for more information.
** Checker plates have a maximum bending angle of 90°.
Stainless steel
All types, except checker plate**
Thickness | Bend angle |
t/m 4 mm | 37° t/m 175° |
5 mm t/m 6 mm | 67° t/m 175° |
10 mm* | 85° t/m 175° |
12 mm* | - |
*For thicknesses of 10 mm and 12 mm, it is not possible to bend full lengths. Please contact Customer Service for more information.
** Checker plates have a maximum bending angle of 90°.
High-strength steel
S355 and CorTen A
Thickness | Bend angle |
t/m 3 mm | 37° t/m 175° |
4 mm t/m 8 mm | 67° t/m 175° |
10 mm* | 85° t/m 175° |
12 mm* | 85° t/m 175° |
*For thicknesses of 10 mm and 12 mm, it is not possible to bend full lengths. Please contact Customer Service for more information.
If the protruding section is longer than 58 mm, then the corner to be bent cannot be smaller than 70˚ due to collision on the lower beam of the bending machine. If the protruding section is not longer than 58 mm, then the maximum angle is 37˚.
Max X = 1390 mm at 90° bending
Minimum distance from hole to bending line
Due to curving and deviations, holes larger than 5 mm may not fall within the leg length of the concerning material type and thickness.
For holes within the minimum leg length, make sure that the sum of the diameters of the holes and/or length of the slots never exceeds 10% of the length of the relevant setting.
Click here for an overview of the minimum leg lengths
If the hole still has to be closer to the bend line, a cut can be made to the bend line. Do not use a radius greater than 1 mm in the corners of the cut.
Conditions for the cutting line:
- Length = minimum length of hole (A)
- Width = 0.8 x sheet thickness (B)
Note: The end of the bend line must be straight, and is also included in the calculation for the maximum break in the bend zone.
If there is a bevel here, we cannot guarantee that the product will meet tolerances. See illustration.
The following points should be considered when designing notches:
- There must be sufficient material in the bending zone to ensure the stability of the part.
- Round cutouts such as slotted holes are often prone to cracking because the material is weakened at the corners.
- The ideal shape for cutting out the bending zone is a rectangular cut-out.
Note: The end of the bending line must be straight, and is also included in the calculation for the maximum break in the bending zone.
If there is a chamfer here, we cannot guarantee that the product will meet the tolerances. See illustration.
Bendable materials
Material | Thickness |
CRS CR4 | 0,8 t/m 3 mm |
HRS 14 HR pickled & oiled | 3 t/m 8 mm |
HRS 50F45 pickled & oiled | 3 t/m 6 mm |
HRS 14 HR | 2 mm |
HRS 46F40 | 3 t/m 8 mm |
HRS 46F40 pickled & oiled | 3 t/m 8 mm |
HRS CorTen A | 1,5 t/m 2 mm |
CRS CorTen A | 3 t/m 5 mm |
AlMg3 EN AW 5754 H111 | 1 t/m 8 mm |
AlMg3 ENAW5754 H111 1sc | 1 t/m 3 mm |
Sendzimir DX51+Z275 | 0,75 t/m 4 mm |
Zincor St12 ZE25/25-03 | 0,8 t/m 3 mm |
Brass CuZn37 HH | 1 t/m 3 mm |
Magnelis S250 + ZM310 | 1 t/m 4 mm |
Material | Thickness |
AISI304L 2B | 0,8 t/m 6 mm |
AISI304L 2B 1s coated | 1 t/m 3 mm |
AISI304L 240Si grit 1s coated | 2 mm |
AISI304L 320Si grit 1s coated | 1 t/m 4 mm |
AISI316L 2B | 1 t/m 5 mm |
AISI316L 320Si grit 1s coated | 1 t/m 3 mm |
AISI430 240 grit 1s coated | 1 mm |
AISI430 finish 2R | 1 mm |
AISI 1.4003 CR finish 2B | 1,5 t/m 2 mm |
AISI 1.4003 HR finish 1D | 3 t/m 4 mm |
Material | Thickness |
AISI304L 2B | 5 mm, 6 mm |
AISI316L 1D | 6 mm |
HRS 14 HR pickled & oiled | 8 mm |
HRS 46F40 | 6 mm |
HRS 46F40 pickled & oiled | 6 mm |
AlMg3 EN AW 5754 H111 | 8 mm |
Collision with tools/machine
The ability to manipulate the material is largely dependent on the tools used. In order to create U-shapes, 247TailorSteel uses special D-tools. In order to prevent the tools from being overworked, the D10 tools are used to bend U-shapes of up to 5 mm for steel and up to 4 mm for stainless steel. 8mm Steel, 6mm Stainless Steel and 6-8 mm High Tensile Steel are bent with an R-10 tool.
Note: However, there is a limit to the feasible width/height ratio of the U shape. See the figures below to determine what the feasible width/height ratio is.
For products as shown in the image, the flange cannot be longer than 32 mm. This is related to the extension (35 mm) of the “horn stamps” that are used to make these types of products.
Large/Conical radii
Large or conical radii must be delivered in segments.
Products with this kind of radius are bent in steps, during which the distance between the bends must satisfy the rules for “minimum leg length”.
If a radius is bent conically using multiple consecutive settings, then the bend lines that meet at a “point” can not be drawn as overlapping.
The figure right shows the minimum sizes of stop lugs for the purpose of large or conical radii.
Our narrowest tools are 20 mm. For bends such as those in the image below, this must be taken into account. This is why there must be enough room present for the mold in order to perform the bend.
From a sheet thickness of 4 mm, the width should be at least 22 mm.
In order to bend settings (into corners) such as those shown below, a cut must be made like the one displayed with the red lines.
This cut must be at least the same width as the side to be set.
The sides to be set (corners) cannot be drawn completely against each other due to our tolerances.
We recommend:
- Up to 3 mm sheet thickness, 0.5 mm space between;
- From 4 to 6 mm sheet thickness, 1 mm space in between;
- From 7 to 8 mm sheet thickness, 1.5 mm space in between.
Always take into account a minimum of 0.5 mm of space between the side to be set and the side that will remain flat.
To be able to process a product, we need at least a 20 mm stop line parallel to the edge, see example.
If it is not possible to create a straight stop line, we can also add ridges. ridges up to a maximum of 40 mm apart (one stop), or at least 200 mm apart (two stops). see image.
At 247TailorSteel it is possible to have hemming set. The delivery specifications are as follows:
Material: aluminum, stainless steel and steel
Plate thickness (T): see table
Minimum leg length (H): see table
Minimum distance to cant (L1): 6 mm
Minimum distance to cant (L2): 13 mm
Types of hemmings:
247TailorSteel only sets closed hemmings.
These minimum distances to cant (L1 & L2) also apply to tilts that are perpendicular to the hemming:
Material | Sheet thickness in mm (T) | Minimum leg length in mm (H) | Minimum distance to hemming in mm (L1) | Minimum distance to hemming in mm (L2) |
Steel / Galvanised steel | 1,00 | 17,0 | 6 | 13 |
1,25 | 15,5 | 6 | 13 | |
1,50 | 14,8 | 6 | 13 | |
2,00 | 14,0 | 6 | 13 | |
Aluminum | 1,00 | 17,0 | 6 | 13 |
1,25 | 15,5 | 6 | 13 | |
1,50 | 14,8 | 6 | 13 | |
2,00 | 14,0 | 6 | 13 | |
Stainless steel | 1,00 | 18,0 | 6 | 13 |
1,25 | 16,0 | 6 | 13 | |
1,50 | 15,0 | 6 | 13 |
After hemming, the total height is 2 to 2.5 times the original sheet thickness (B). The tolerance A is ± 1 mm, this may result in holes not being straight across from each other. See image "Tolerances".
Hemming may cause cracks, prints or damage in/on the material. This is beyond our control.