Published on: 30 June 2025
Thread tapping in Sophia®
In this edition, we explain how screw threads are tapped. We discuss the following questions:
- What is thread tapping?
- What is thread tapping used for?
- What is the difference between tapping and threading?
- How can I set up tapped holes in Sophia®?
- How are threads tapped?
1. What is thread tapping?
Thread tapping is a metalworking process in which an internal screw thread is cut in a pre-drilled hole. This is done using a special cutting tool known as a tap, which cuts away the material around the hole to create a screw thread structure. This process makes it possible to screw bolts or screws into the hole.
2. What is it commonly used for?
Thread tapping plays a major role in the manufacturing industry. The tapped threaded holes are used to join parts together with bolts and sometimes nuts. The possible uses include structural beams, machine parts and cases for electronics. The technique is used in almost every industry.
3. What is the difference between tapping and threading?
With tapping, an internal screw thread is formed in a drilled hole in a metal sheet, circular, square or rectangular tube or profile etc. Threading means cutting an external screw thread on a cylinder, for example a bolt, bar or round tube.
4. How can I set up tapped holes in Sophia®?
247TailorSteel can tap screw threads in your cut and bent sheet metal parts as an additional processing step. You can indicate this as follows:
- Draw the holes with the correct diameter in your drawing package.
The table below shows the various M sizes with the associated drilling diameter, pitch (distance that a screw travels in a single revolution) and the minimum and maximum sheet thickness.
Thread size (M) Drill diameter (mm) Pitch (mm) Minimum thickness (mm) Maximum thickness (mm) Steel (nitrogen) Staal (oxygen) Stainless steel Aluminium M3
2,5
0,50
1,0
4
6
5
4
M4
3,3
0,70
1,4
4
6
12
4
M5
4,2
0,80
1,6
5
6
15
6
M6
5
1,00
2,0
6
8
20
8
M8
6,8
1,25
2,4
8
15
20
8
M10
8,5
1,50
3,0
8
15
20
10
M12
10,2
1,75
3,0
8
15
20
10
M14
12
2,00
4,0
8
20
20
10
M16
14
2,00
4,0
8
20
20
10
M18
15,5
2,50
5,0
8
25
20
10
M20
17,5
2,50
5,0
8
25
20
10
M22
19,5
2,50
5,0
8
25
20
10
M24
21
3,00
6,0
8
25
20
10
- Upload your DXF/DWG or STEP file in Sophia®.
- Go to the product visualisation or open the 3D view of the part.
- 4. Select the hole you wish to have tapped by clicking on the pin, which will turn green.
TIP: Do you wish to select several holes? Keep the Ctrl key pressed and click on the pins you wish to select, or keep the Shift key pressed and drag the cursor over all the pins to select them.
5. Mark the pin as a ‘Tapped hole’ in the dropdown menu. It will now turn red.
6. The hole will automatically be assigned the correct M size.
7. If desired, you can check the M size by moving your cursor over the red pin.
If one or more of the selected holes has an invalid diameter, a warning will appear:
If at least one of the holes can be marked as a tapped hole, you can continue marking tapped holes despite the warning. The holes with valid diameters will be marked as tapped holes and the holes with invalid diameters will not.
Finally, we wish to point out that thread tapping is only possible with:
- Flat and bent sheets.
- Maximum product sizes of 1000x1000 mm or 2000x500 mm.
- Products with a maximum weight of 40 kg.
5. How are threads tapped?
Screw threads can be tapped in two ways:
- By hand
- With a machine
Hand tapping is usually used for small or single holes where there is limited space for tools to be placed and moved. While a machine requires more space, it is more suitable for large-scale production. The essence of both techniques is the same, only the tools are different.
At 247TailorSteel, we use machine tapping.
The metal is often marked first with a punch or laser to show where the hole should be drilled.
The correct drill and screw thread are chosen based on the desired diameter using the metric dimensions in the table above.
The hole is drilled to the chosen diameter. This hole is always smaller than the final diameter of the screw thread, as metal must remain to be cut with the tap. The thread is cut into this ‘extra’ metal at the edge.
In fact, we don’t drill the holes – we laser cut them directly while the sheet metal is being cut to size by the machine.
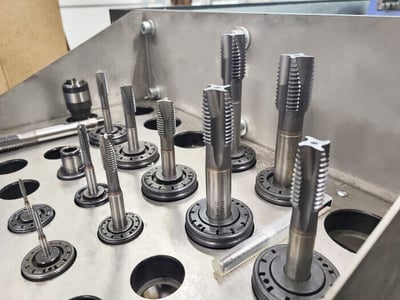
We then place the part on the tapping table and position the tap with the correct size (M3, M4 etc.) directly above the hole. We lubricate the tap with cutting oil to reduce friction between the tap and metal. This ensures a smoother cut and reduces the force on the tap.
Finally, we introduce the tap into the hole with a turning movement. While this can be done by hand, we use a tapping machine, also known as a tapping table.
Do you have any questions about thread tapping?
We have written this Feature Friday to make working with Sophia® even easier and more efficient. Thanks for your time and see you next Feature Friday. If you have any comments or questions, please contact us.
Latest news always in your mailbox?
Sign up for our newsletter and we will deliver the latest news and offers directly to your inbox.