Published on: 14 July 2025
Everything you need to know about the bend radius of sheet metal
Bending sheet metal involves a lot more than just forming curves and sharp corners. An important parameter that affects the strength, durability and appearance of sheet metal is the bend radius. In this blog post, we answer the following questions in greater detail:
- What is the bend radius?
- Why is the (minimum) bend radius important?
- How can I calculate the minimum bend radius?
- Which factors affect the bend radius?
1. What is the bend radius?
When bending sheet metal, the bend radius is actually just the length of the inside of the bend, from the point where the bend starts to the point where it ends. The image below shows a piece of sheet metal bent to an angle of 90 degrees (of course the angle can also be larger or smaller). The dark blue part is the bend radius.
The inside of the bend is called the inside radius. The outside of the bend is called the outside radius. An imaginary line known as the neutral axis passes through the centre of the sheet.
When we refer to the bend radius, we actually always mean the inside bend radius. This is the most stable, as it is formed around the edge of the punch. In contrast, the outside radius can deviate more and isn’t always perfectly round.
2. Why is the (minimum) bend radius important?
In fact it isn’t really the bend radius that is important, but the minimum bend radius.
When you bend metal, you change the length of the metal on both the inside and outside of the bend. The inside is compressed and the outside is stretched.
This deformation can reduce the strength of the metal and cause cracks. This is why the minimum bend radius is so important. It is the ‘smallest’ inside radius that can be achieved without the metal losing strength or cracking.
3. How can I calculate the minimum bend radius?
We are often asked how the minimum bend radius can be calculated. While formulas are available, it is important to understand that many factors affect the bend radius. All these factors make using the most accurate formula very complex and error-prone.
This is why we have implemented the formula in our online software Sophia®. Based on your drawing, chosen material type and all these additional factors, Sophia® automatically determines whether your chosen bend radius is feasible. If not, you will be shown a warning after just a few seconds.
We recommend always using software or consulting tables with exact values, as shown below:
Internal radius 90 degrees
Material thickness | Steel | Stainless steel | Aluminium | High-strength steel |
0,8 mm | 1,39 | 1,56 | - | - |
1 mm | 1,40 | 1,58 | 1,27 | - |
1,25 mm | 1,42 | 1,57 | - | - |
1,5 mm | 1,65 | 1,90 | 1,47 | - |
2 mm | 1,88 | 2,22 | 1,67 | - |
2,5 mm | 2,41 | 2,94 | 2,11 | - |
3 mm | 2,75 | 3,75 | 2,50 | - |
4 mm | 3,02 | 4,48 | 3,30 | - |
5 mm | 3,62 | 7,82 | 4,07 | - |
6 mm | 4,62 | 11,91 | 5,34 | - |
8 mm | 8,00 | 11,64 | 8,12 | 8,00 |
10 mm* | 8,00 | 15,00 | - | 8,23 |
12 mm* | 7,83 | - | - | 7,02 |
Internal radius sharp
Material thickness | Steel | Stainless steel | Aluminium |
0,8 mm | 1,41 | 1,72 | - |
1 mm | 1,35 | 1,62 | 1,28 |
1,25 mm | 1,27 | 1,52 | - |
1,5 mm | 1,19 | 1,42 | 1,12 |
2 mm | 1,30 | 1,59 | 1,22 |
2,5 mm | 1,73 | 2,17 | 1,61 |
3 mm | 2,51 | 3,73 | 2,86 |
4 mm | 2,24 | 3,28 | 2,48 |
5 mm | 2,45 | 5,44 | 2,70 |
6 mm | 3,08 | 8,78 | 3,53 |
8 mm | 4,74 | - | 4,33 |
* For thick 10 mm and 12 mm plates, it is not possible to edge full lengths.
Please contact Customer Service for more information.
You can read all our guidelines for sheet metal bending here.
If you are nevertheless interested in a formula to calculate the bend radius, then we are happy to share the following, commonly used (although simplified!) formula to calculate the mini-mum bend radius:
Minimum bend radius = K x t
The K stands for a constant or factor, which depends on the type and thickness of the metal. It varies between 0.5 and 2.
The t stands for the thickness of the metal.
Here is an example calculation to illustrate how this works.
Imagine you wish to bend a 3 mm thick stainless steel sheet. The constant for stainless steel that is 3 mm thick is approximately 1.25. You can easily calculate the minimum bend radius by multiplying the constant (1.25) by the thickness (3 mm). The result is 1.25 x 3 = 3.75. If you wish to bend this stainless steel sheet without cracking, the bend radius must be at least 3.75 mm.
Once again, this is just a guideline. Please be aware of this. The exact value may differ due to other factors that affect the bend radius. We therefore recommend that you always follow the guidelines for bending.
4. Which factors affect the bend radius?
The following factors may affect the bend radius:
- Material thickness
- Bend angle
- Punch radius and groove width of the die
- Metal type and properties
- Rolling direction
- Technique used (free bending and forming/stamping)
We explain each of these factors in greater detail below.
Let’s start with the thickness of the metal sheet. Imagine the following situation. You have a sheet of A4 paper that you wish to bend. It should be easy to create a smooth, sharp fold. Now try the same with a stack of 100 A4 sheets. It will be much more difficult. The thick stack of paper can be bent, but it won’t be easy, and the fold line will not be so sharp. The same applies to sheet metal. The thicker the sheet, the more difficult it is to achieve a small bend radius without the metal cracking. This is why the thickness of the metal often determines the minimum bend radius.
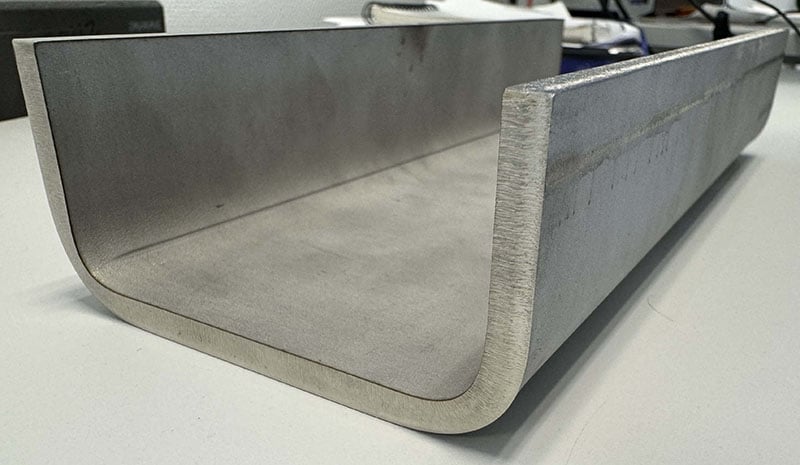
The next factor that affects the bend radius is the desired bend angle. Bends are often made to an angle of 90 degrees. However, the angle may be wider or sharper. This also affects the bend radius. The sharper the angle is, the further the stretched side must be stretched.
The punch radius and the groove width of the die also affect the bend radius. The larger the radius of the punch and the wider the die opening, the larger the inside radius of the workpiece will be.
The metal type and properties are also important. Depending on the exact alloy, every metal type has certain properties, including hardness and toughness. As you can imagine, a metal that is hard will also not bend as easily, and if you apply a large force in an attempt to bend it, there is a risk that it will break instead of bending. In conclusion, the minimum bend radius required to avoid cracking also depends on the metal used, and in particular its properties.
Finally: the rolling direction of the metal. Metal is often transported as coils before being rolled flat and stretched on location. This process results in a structure with elongated grains in the rolling direction.
If we bend the metal in parallel to these elongated grains, the metal will be more likely to crack than if we bend it perpendicular to the grains. This means the minimum bend radius is larger if you wish to bend the metal in parallel to the rolling direction and that it can be smaller if the metal is bent at right angles to the rolling direction.
Cut sheet metal parts may have bends that are both parallel and perpendicular to the rolling direction. In this case, both bend types will be made with the same tooling, and the minimum bend radius of the weakest form (bends in parallel to the rolling direction) will always be used, even though the bends that are perpendicular to the rolling direction can be made with a smaller bend radius.
Would you like to know more, or do you need more advice?
Please contact our Customer Service. We will be happy to assist you!
Latest news always in your mailbox?
Sign up for our newsletter and we will deliver the latest news and offers directly to your inbox.